Edge Welded Metal Bellows Seals Designed and Manufactured in the U.S.A.
Flexaseal Engineered Seals and Systems, LLC is a world leader in engineering and manufacturing edge welded metal bellows seals and devices that can reliably operate in a wide range of applications and temperatures. Our standard metal bellows can operate in conditions up to 400° F, while high-temperature metal bellows can reliably handle up to 800°F. Flexaseal also specializes in cryogenic bellows seals and specially engineered metal bellow devices for vacuum applications.
For all cryogenic, compressor, and centrifuge sealing options as well as other engineered bellows inquiries, please contact our applications team. In addition to bellows component seals, our edge welded metal bellows devices are also used in many of our standard and special cartridge seal designs.
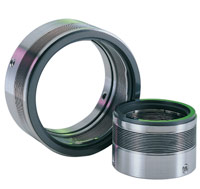
40/42/45
Low-Temperature Edge Welded Metal Bellows (Up to 400°F)
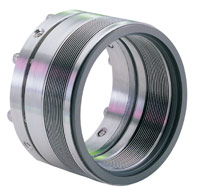
60/62/64/65
High-Temperature Edge Welded Metal Bellows (Up to 800°F)
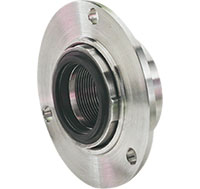
Cryogenic Seals
Hermetic Bellows
Quick Contact
For general inquiries, sales or quotes.
WELDED BELLOWS FAQ’S
Yes, Flexaseal’s edge-welded bellows are completely manufactured at our Vermont factory. Our welding department and engineering staff work closely together to control the manufacturing quality of all bellows assemblies, from stamping sheets of foil stock through welding cores and end fittings, evaluating spring rates, and pressure testing the completed assembly. We use the TIG (Tungsten Inert Gas) welding process which provides the finest control of the weld arc, resulting in efficient, clean, and long-lasting welds.
There are two main classifications of bellows: edge-welded and formed.
Formed bellows are manufactured from either welded (seamed) or seamless tubing and utilize extensive automation for mass production. This process offers some cost benefits over edge-welded bellows assemblies however, formed bellows are limited to materials which can be elongated through either rolling or hydroforming. Formed bellows typically have thicker convolution structure with higher spring rates and larger deviations than edge-welded bellows which impacts precision loading.
Flexaseal designs and manufactures edge-welded bellows. Our bellows production begins by stamping male and female diaphragms from sheet (foil) stock. We inventory foil stock including various Hastelloy™ and Inconel® grades, titanium and Monel® as well as cryogenic-grade materials, to accommodate a wide range of applications. Diaphragms are TIG-welded together to create a convolution, and these convolutions are assembled together and welded to create the bellows core. Bellows core sizes can range from just a few welded convolutions to 100+ convolutions for a hermetic bellows assembly.
Contrary to popular belief, it is possible to repair a rotary bellows assembly. If pressure testing reveals leakage around the seal face, Flexaseal will de-insert the current face and check the retainer for any damage. If the retainer is within the necessary tolerances, FAS will insert a new face into the assembly as well as replace the other wear parts (O-ring and hardware).
If the bellows rotary shows visible damage to either the bellows core or end fittings, or a pressure test reveals leaks in the assembly itself, Flexaseal recommends a new bellows assembly to ensure sealing integrity.
In either option, all bellows assemblies are always pressure-tested and lapped to the required flatness before leaving our factory.
In a pusher seal design, the secondary sealing component – usually an O-ring or a wedge — must move axially to compensate for wear, vibrations, and movements of the shaft.
A bellows rotary eliminates this dynamic secondary sealing component, which means
- No material build-up on the shaft which can “hang up” a dynamic O-ring, causing fretting, shaft damage, and seal failure
- The flexing action of a bellows rotary is more forgiving of axial movement and vibration
- A bellows rotary is far less likely to “take a set” from heat or chemical attack
Welded bellows assemblies also offer the benefit of an inherently balanced seal design. Mechanical seal balance refers to the ratio of the opening and closing areas of the seal faces. Both a balanced and unbalanced design may have the same opening face area but the balanced seal’s closing area is smaller, reducing the load on the faces. This reduced load means less heat generated at the seal faces, enabling the balanced seal to run cooler than an unbalanced seal design. This cooler operating environment positively impacts a seal’s run time.
If your facility must comply with API Standard 682 which requires all Type B or C cartridge seals to utilize a balanced seal design, standardizing on hydraulically balanced, welded metal bellows seals ensures satisfactory seal run time and low seal maintenance for your equipment.
First, a few definitions –
Free length (FL) – Uncompressed axial length of a bellows assembly. The term can also refer to the free extended length of a bellows assembly.
Operating length (OL) – also referred to as installed or working length: The axial length of a bellows assembly as installed to the designed compression. The term may also refer to the dimensional range within which a bellows assembly can safely be operated.
Mechanical seals, whether a pusher or bellows design, need a specific amount of compression to ensure the faces are in contact to maintain the correct amount of lubrication to operate (dry-running seal designs are the exception to this statement.) Both the Free Length and Operating Length are necessary for this compression calculation: Free Length – Operating Length = amount of compression. Here’s an example: