At Flexaseal, we engineer mechanical seals that do more than just prevent leaks; they are a cornerstone in the optimization of your rotating equipment: process pumps, API pumps, chemical pumps, slurry pumps, mixers, reactors, vessels, and many more. Our seals are crafted within the precision-driven landscape of American manufacturing, ensuring each product not only meets but exceeds the operational demands across diverse industries.
Mechanical Seals for Pumps and other Rotating Equipment
Precision-Engineered Mechanical Seals: Solutions for Optimizing Rotating Equipment Performance in Diverse Industries.
ANSI
ANSI Seals
Designed for the diverse requirements of the processing industry, Flexaseal’s ANSI Seals are the answer to the common challenge of maintaining seal integrity in fluctuating conditions. They are engineered to provide a reliable seal, reducing maintenance frequency and costs.
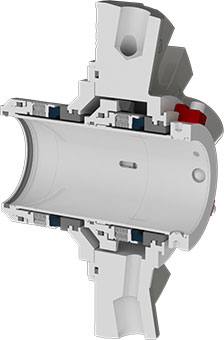
API
API Seals
In the high-stakes environment of the oil and gas industry, our API Seals stand up to extreme pressures and temperatures. They are not just seals; they are a safeguard, ensuring environmental compliance and operational continuity.
Split
Split Seals
The Flexaseal split seal is a game-changer for industries where downtime equals lost revenue. They are designed for quick installation and maintenance without the need for equipment disassembly, addressing one of the most significant pain points in seal replacement.
Slurry
Slurry Seals
For industries grappling with abrasive and corrosive fluids, our flushless slurry seals are the frontline defense, offering robust construction that extends the life of both the seal and the equipment.
Component
Component Seals
Flexaseal provides component seals for a wide range of challenging applications where cartridge seals are impractical or incompatible with current rotating equipment.
Mixer
Mixer Seals
Tailored for the unique demands of mixing applications, Flexaseal’s Mixer Seals ensure product purity and consistency. They solve the common issue of cross-contamination, which is critical in the pharmaceutical and food industries.
Gas
Gas Seals
With a focus on environmental safety and regulatory compliance, our Gas Seals provide a high-integrity sealing solution for applications where even the smallest leak is unacceptable.
Improve the Reliability of Your System
Elevating seal reliability and performance, our solutions are engineered to withstand demanding conditions, significantly reducing downtime and maintenance. We blend innovative design with superior service to extend the lifespan and integrity of your equipment. Experience a new standard in reliability, where advanced technology meets customer-focused support.
Mechanical Seals Products
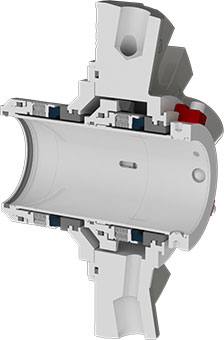
ANSI Mechanical Seals
API Seals
Split Cartridge Seals
Single Cartridge Seals
Edge Welded Metal Bellows
Dual Cartridge Seals
OEM Replacement Mechanical Seals
Slurry Pump Seals
Engineered Component Seals
Mixer/Agitator Seals
Gas Mechanical Seals
Multi-Lip Cartridge Seal
Quick Contact
For general inquiries, sales or quotes.
Mechanical Seal FAQ’s
Mechanical seals are critical components in various industrial applications, ensuring the effective and safe operation of machinery. However, like any component, they can fail due to a variety of reasons. Understanding these causes is key to preventing downtime and maintaining system integrity. Here are the common causes of mechanical seal failures:
- Improper Installation: Incorrect installation can lead to uneven loading, misalignment, and eventual seal failure. It’s essential that seals are installed following the precise guidelines set out in Installation, Operation, and Maintenance (IOM) Manuals.
- Incorrect Material Selection: The choice of material for seal faces, wetted metal components, and O-rings or secondary seals is crucial. Incorrect materials can be vulnerable to the media they are exposed to, leading to corrosion or wear.
- Operational Issues: Fluctuations in pressure, temperature, or speed beyond the seal’s design specifications can compromise its integrity. Operating conditions must align with the seal’s capabilities.
- Chemical Attack: Exposure to aggressive chemicals can degrade seal materials. The compatibility of seal materials with the process fluid is vital for seal longevity.
- Abrasive Particles: The presence of abrasive particles in the process fluid can erode incorrectly selected seal faces or other wetted components, leading to premature failure.
- Thermal Extremes: Exposure to temperatures outside the operational range of the seal material can cause thermal deformation or cracking.
- Vibration and Misalignment: Excessive vibration and misalignment of the pump shaft can impose undue stress on mechanical seals, hastening wear and failure.
- Dry Running: Operation without adequate lubrication across the seal faces can cause excessive heat and wear, leading to seal failure.
At Flexaseal, we design our seals to address these challenges, offering robust solutions tailored to diverse operational environments. Our expertise ensures that each seal not only fits your specific application but also combats the common causes of failure, enhancing reliability and efficiency.
Yes, you can repair mechanical seals, often at a lower cost than buying new ones. At Flexaseal, we efficiently restore seals to like-new condition, offering substantial savings over your equipment’s lifetime.
Our repair services aren’t limited to our own products. We can repair any brand of seal, thanks to our robust reverse engineering capabilities and extensive catalog of technologies and designs. We thoroughly evaluate each seal, replacing or refurbishing essential parts to ensure optimal performance.
Choosing to repair with Flexaseal means your seals will function as effectively as new ones, but without the expense of a full replacement. This approach not only saves money but also extends the life of your rotating equipment, ensuring its ongoing effectiveness and reliability.
Yes, split seals can be as reliable as cartridge seals when used in the appropriate applications. Flexaseal’s split seal technology is designed for ease of installation and maintenance, particularly in situations where disassembling equipment to change a seal is impractical or costly.
Our split seals are engineered for high reliability, matching the performance of traditional cartridge seals in many applications. They are particularly advantageous in larger equipment, where cartridge seals might be difficult to install due to their size and weight.
While cartridge seals are often chosen for their pre-assembled, easy-to-install design, our split seals offer a comparable level of sealing effectiveness and longevity, with the added benefit of simpler installation in challenging or restricted spaces. This makes them a versatile and reliable choice in a wide range of industrial settings.
Enhancing the lifespan of your mechanical seal involves several key practices:
- Proper Installation: Ensure that your mechanical seal is installed correctly. Incorrect installation can lead to premature failure. Always consult your Installation, Operation, and Maintenance (IOM) Manual, or call your Flexaseal representative for advice!
- Appropriate Material Selection: Choose materials that are compatible with the media and operating conditions. Using the right materials can significantly extend the life of the seal.
- Regular Maintenance: Routine inspections and maintenance can help identify and rectify issues before they lead to seal failure.
- Operational Parameters: Operate your equipment within the specified limits for pressure, temperature, and speed to avoid overstressing the seal.
- Use of Support Systems: Implement appropriate seal support systems, like filtration or cooling, to maintain optimal conditions for seal operation.
At Flexaseal, we also offer expert guidance and support to help you select and maintain the right seal for your specific application, further ensuring the longevity and reliability of your mechanical seals.
Contact us today!